Cars I’ve Worked On
I’ve been a car fanatic since I was a young lad. It started in high school with my first Mustang, then buying parts cars and modifying my cars. Then my uncle opened a body shop with another guy who was a car restoration expert, and a painter in the pilot plant at Ford. I got a job working there, first painting the walls of the plain block building white, and then as a helper and learning how to do body work and painting.
When I got into automotive engineering, lessons I learned in restoring cars and replacing body sheet metal went a long way towards being one of the pioneers in the field of Dimensional Management, where I specialized in body structures – how to build a car so that everything fit together properly. During that stage of my career, in addition to working on pick-ups, family cars and minivans, I got to work on some pretty cool cars.
After I moved to Florida, I bought a car repair shop and spent a couple of years repairing European sports cars and also used car sales.
Through it all, I’ve had a chance to work on some pretty cool cars! Here are the highlights
The Engineering Years
As an automotive engineer, I worked on some interesting vehicles from an engineering perspective, even if they won’t go down in the annals of automotive history. First was designing all of the floor coverings for the Chevy Astro van, followed by moving into Dimensional Management on the full-size GM pick-up. That led to doing the Olds Custlass, Pontiac Grand Prix, Chevy Lumina and Buick Regal. While they were engineering masterpieces with four-wheel disc brakes and body structures that were a significant leap forward, I remember seeing the first actual cars on a hauler and I was disappointed at how plain they looked.
Next it was over to Chrysler where things got really interesting. In addition to overseeing a team of engineers working on every car project, I personally worked on the “cool” cars at Chrysler at that time: Viper, Prowler, Chrysler Concept Vehicle.
Dodge Viper
When the concept Viper was displayed at the Detroit Auto Show, car enthusiasts went nuts. People sent deposit checks to Chrysler Corp. I got the opportunity to work on the body panels and spaceframe for this car, and had three engineers under me working in the plant. They passed stories to me about driving the fully built spaceframe – the complete car without the body panels – outside the plant. The original assembly plant was in a former plant building that was sitting empty and they put the short assembly line and dyno in the front. When the bosses weren’t around, the few engineers would take a fully drivable spaceframe and wank on it on the side of the plant. I still have my Team Viper jacket and a numbered print by the illustrator on the program.
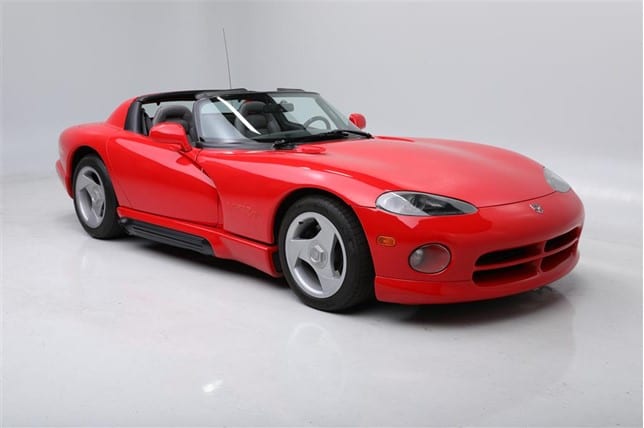
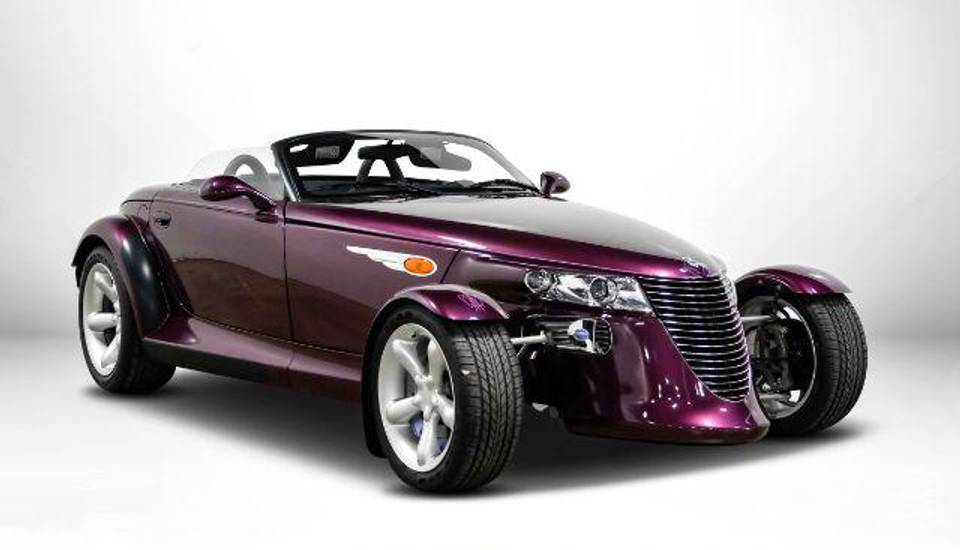
Plymouth Prowler
While the Plymouth Prowler has never been known for blistering performance, only powered by a standard V6 engine, the styling is rad for an American production vehicle. Fitting all of the emissions and electronics under that hood was no easy matter, and getting everything to fit was equally as challenging. It was a fun project to work on.
Chrysler Concept Vehicle
The Chrysler Concept Vehicle was a concept for third-world production. How could one make a simple, inexpensive vehicle for third-world countries? It was a design and engineering study on how to build a plastic-bodied car with four major body panels (left outer, left inner, right outer, right inner) plus connecting pieces, doors and hood. The highlight for me was presenting my work to the chairman and VPs of Chrysler. Shortly afterwards, Chrysler “merged” with Mercedes-Benz, forever sealing the fate of CEO Bob Eaton as the anti-christ within Chrysler and the project died in the “merger.” But it was a very cool project, with these huge injection-molded body panels made out of recycled plastic and an engineering challenge for me as well.
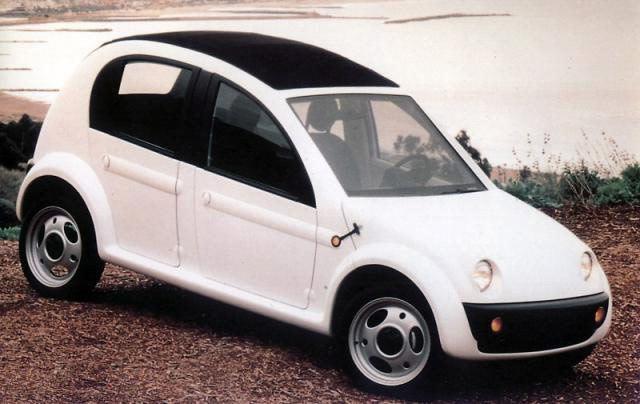
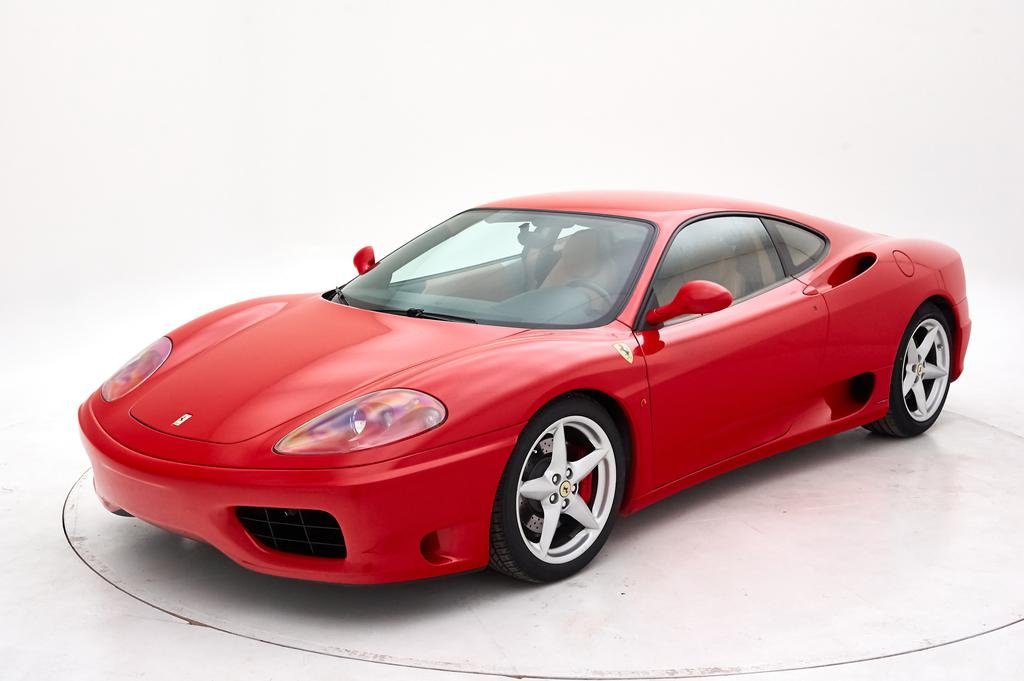
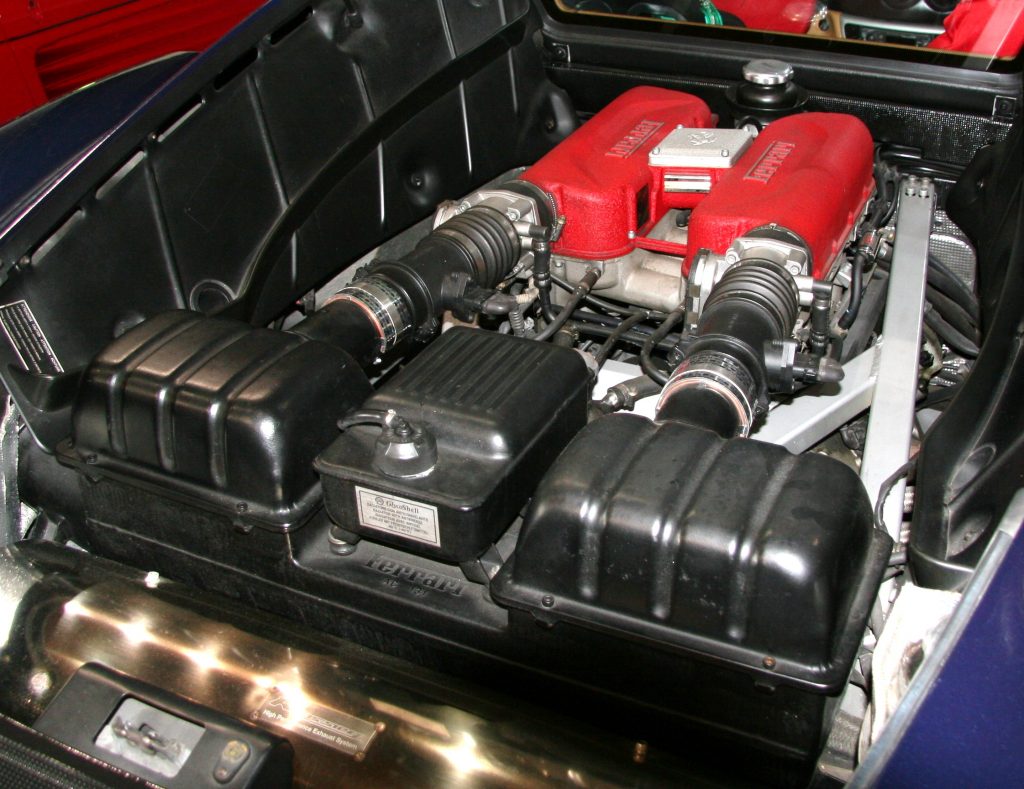
Ferrari F360 Modena
Without a doubt, the highlight of my automotive engineering career was working on the Ferrari F360 Modena. The consulting company I was working for started doing work for Alcoa, who had landed the contract to design and build the aluminum spaceframe for Ferrari. We were brought in to help Alcoa design and build the spaceframe so that everything fit properly – parts were where they were supposed to be and not too big, too small, or assembled out of position. And do it every time without having to manually finesse or rework the bodies.
I had two engineers under me on the project, one of whom got to spend a year in Italy in the Ferrari plant launching the vehicle. I got a plaque from Alcoa with some very nice words on it. I’d trade that for a year in the Ferrari plant any day.